MILLING ON CHEVALIER
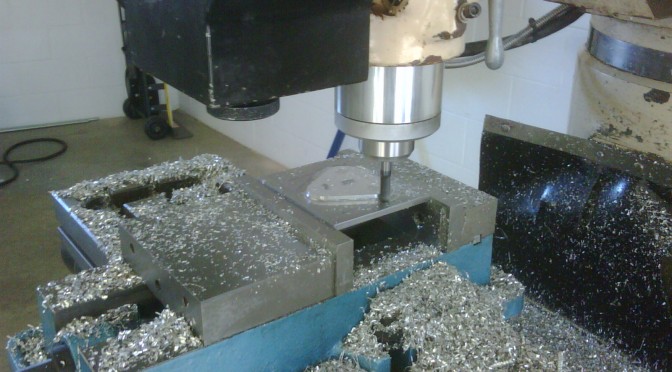
The headline of this article is that China’s development of a possible stealth fighter (and an anti-carrier cruise missile) has caught the US off guard. I really don’t see why: the US has not put enough emphasis on engineering education and manufacturing in some time. Instead, we have allowed manufacturing jobs to dwindle and go overseas.
Economists, many of them anyway, say this is good for the US consumer, because it results in lower prices for goods. That may be true in some regards, but it also leaves us lacking in technical prowess. This country didn’t rise to prominence based on military might, at least not solely; it rose to prominence on technical innovation. We built the best stuff, simply put. But if we let our manufacturing continue to disappear, there won’t be any people left to design the best stuff. People who don’t know how to do anything hands on don’t design products; engineering takes knowing how things work, and you really only learn that, REALLY learn that, by doing.
I am not an unabashed military technology junkie, or might is right kind of guy; I’m just a realist. The wars of the future will continue to involve more and more military technology. As drones, robots, computers and the like take center stage, the country best likely to win is the one with not just the best soldiers, but the one with the best engineers. Right now, over 85% of the world’s engineers live in Asia.
This is not an article to bash China. China has every right to develop weapons to protect their interests, just as the US does. They have every right to develop their economy as they see fit, and in the most profitable way. We need to get our heads out of the sand and get back on the work that made America great, before we are just another page in the book of fallen empires. That’s just my view from the machine shop!
Doing a little reading at the machine shop.
The Washington Times recently reported on aircraft carrier-based drones for the Navy. It’s an interesting look at an emerging military technology. The drones are still in the early stages, and aren’t expected to be fully operational for a few years at least. Still, Skynet will be complete very soon…
I needed to turn some custom parts with a hose barb on one end. This wouldn’t be very hard on a CNC lathe, but I only had a manual lathe. To make a custom shape like this, a form tool is used. This isn’t a technique I invented, obviously. To get my part shape, I had a custom form tool cut by a wire EDM machine at another shop.
To use the tool, I roughed the form close and then plunged the tool in to finish the barb form. It made quite a lot of noise, which might have meant the tool was over center a bit. It was a little hard to set the height. I got the parts done, none the less.
The first thing a machinist asks when making a part is, “how do I hold it?” A lot of times a vise or collet chuck is a good answer. There are a lot of techniques. For holding a flat part, often a good answer is to bolt the part to the table or a surface plate. There are a variety of ways to hold a part down, of course. This is an example of one method for holding a flat part for CNC machining. The technique here is more in using my CAM system to make tabs to retain a fully contoured part.
I needed to make some flat manifold plates for a customer. These were to be CNC milled out of 1/4 inch aluminum. The first step was to determine how they were to be held in my CNC. The problem here is that the parts need to be profiled inside and out, making vise clamping or the like unfeasible. As the parts do have bolt holes in them, I could have held the material down with clamps and then pre-drilled the bolt hole pattern. Then, I would have tapped holes in the fixture plate (which is just a scrap of aluminum I use for these sorts of projects) and bolted the material down. The only potential problem with that is that the bolts could mark the surface on the parts. I decided instead to put bolts into the material that would be cut away during machining.
By not using the bolt holes in the part, when I finished machining this job the part would not be held by anything. That is a great way to throw it through a safety shield and bust an endmill. Not good. I used a technique where the part would be held with thin tabs at intervals around the part. My CAM system has the ability to put those in automatically, but if you are manually programming or editing g-code, all you would need to do is pick a spot on the final depth and have the cutter jump up. In this case, I used .025 as a tab thickness, and half inch wide.
Notice that the part stays together with the remainder material even after I unbolt it.
You have to be careful when choosing your tabs; if they are too thin, they will break during machining and the part will move, possibly wrecking it or damaging something else. If they are too thick, it will be difficult to remove the part from the stock. It should be noted also that the endmill moving up the side of the part like that WILL leave a witness mark. In this case, it really didn’t matter. This could have been minimized by having the CNC make more passes around the part, and then a finish pass that only skimmed over the tabs. The machinist has to decide what’s important for those considerations; I chose speed.